
Lugares de interés
Ferrería de Tejedo de Ancares
PRÓXIMA APERTURA.
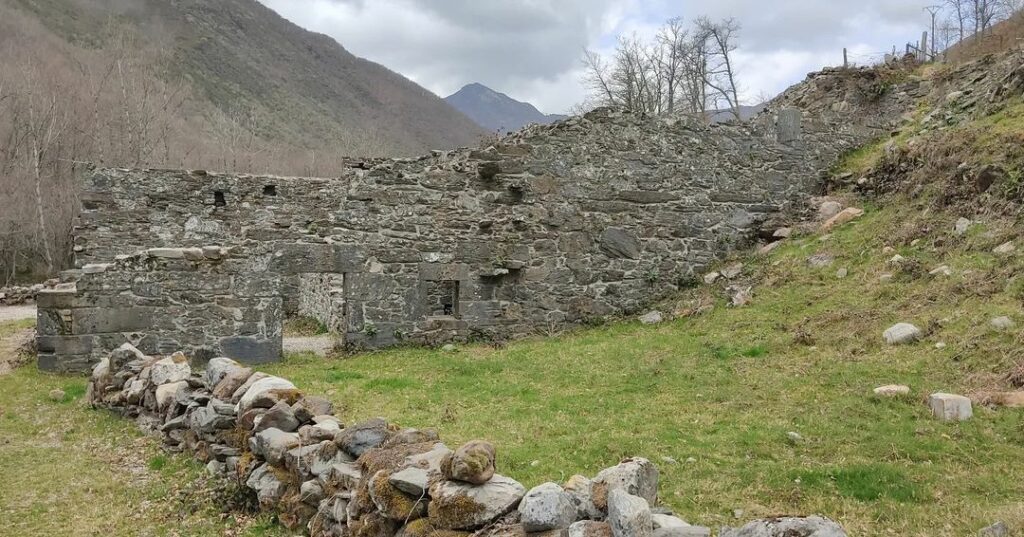
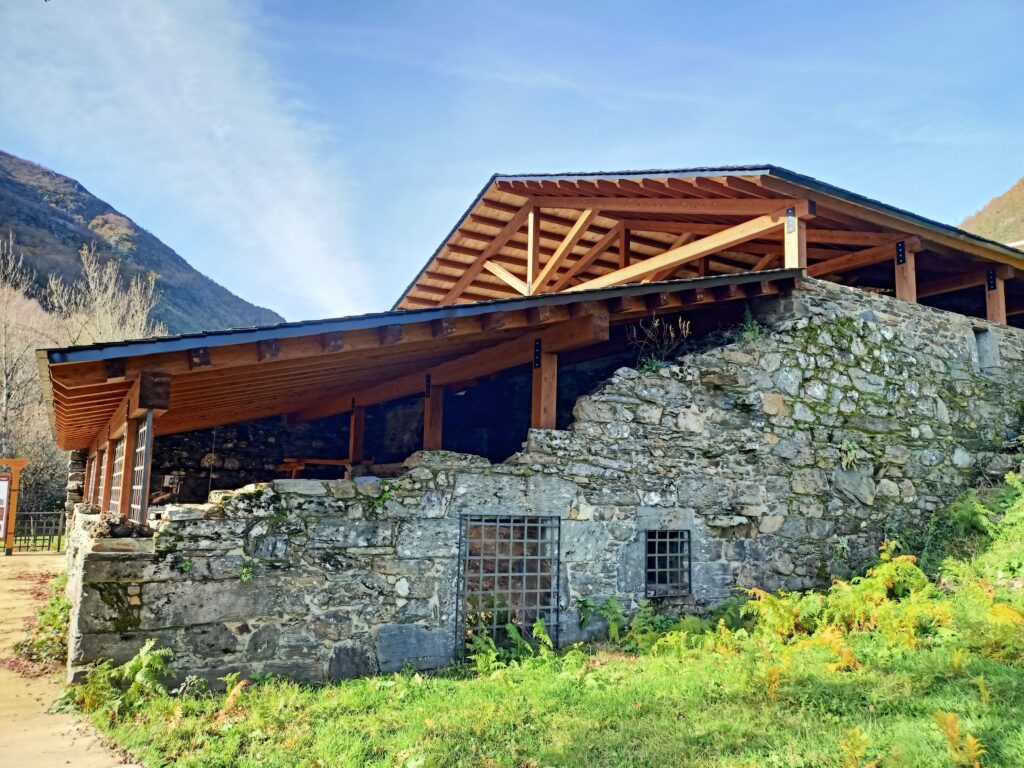
HISTORIA
En agosto de 1788 el concejo de Tejedo y de Pereda de Ancares da permiso para la construcción de “A FERREIRÍA” (llamada así por los lugareños), a don Bernardo y Gerónimo Rodríguez vecinos de Pereda de Ancares y don Francisco Abella vecino de Tejedo de Ancares, todos ellos comerciantes en el Ferrol. Este consentimiento se da por tener “superabundantes montes para coadyuvar a la perpetua existencia de la propuesta fábrica” y por ser de gran utilidad “a nosotros y demás naturales y residentes en este pueblo y demás de este Real Valle”. A finales de agosto se realiza una escritura de convenio entre Bernardo y Gerónimo Rodríguez y Francisco Abella, el cual, cede el prado llamado “el Carrizal” a orillas del río donde se construye la ferrería.
En 1799, se hizo un reparto de los bienes de la ferrería entre sus respectivos herederos. Según la tasación hecha por don Miguel Antonio Uría, maestro arquitecto y director de la herrería de la compañía de la Vega de Ribadeo, el valor de la ferrería ascendía a 135.270 reales con 33 maravedís.
A partir de 1802, los herederos de Bernardo y Gerónimo Rodríguez, aparecen como dueños de dicha ferrería en un arrendamiento. “Todo el artefacto y fábrica de fierro que tenemos sita en término y dezmario del lugar de Texedo a nosotros tocante y perteneciente, que se nos ha adjudicado por parte de los herederos de don Francisco Abella”.
Se sucedieron varios arrendamientos hasta que en 1820 aparece como dueño de la ferrería, por compra, don Juan Francisco Ribadeneira y Pardo, vecino de Santa Eulalia de Teyllar y caballero maestrante de Ronda, conocido en Ancares con el sobrenombre de “El Marelo” debido a su tez clara. En 1859 la ferrería fue vendida tras su muerte violenta. Engañado y traicionado por su amante fue asesinado en lo alto del prado de la ferrería por tres vecinos de Tejedo de Ancares por negarse a dejar pasar una acequia de riego por una finca de su propiedad. Se desconoce con exactitud la fecha exacta de su paralización aunque se calcula que fue entre finales del siglo XIX principios del siglo XX.
Hacia 1905 fue adquirida por Aquilino Barcia y su mujer Inés Rodríguez vecinos de Tejedo de Ancares por 12.000 duros. En 1953 la familia Barcia la vende en 350.000 pesetas a sus actuales dueños. En 2018 se firma un convenio de cesión del uso entre los actuales dueños y el Ayuntamiento Valle de Ancares con la finalidad de su recuperación, promoción y puesta en valor.
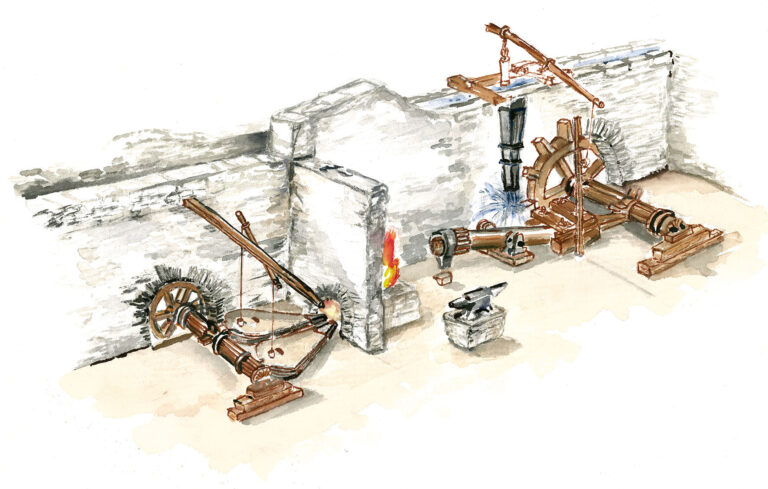
FUNCIONAMIENTO
La ferrería, “fábrica de hierro” era un lugar donde se obtenía el hierro a partir del mineral en bruto.
Esta ferrería utilizaba la fuerza de un salto de agua para accionar el mazo y el sistema de alimentación de aire.
Mediante una presa se captaba parte del agua del río para su derivación hacia el canal que transportaba el agua a la ferrería. El tramo final del canal se ensanchaba para actuar como depósito regulador “banzado” del caudal para la ferrería. La parte final la constituía el “banzadillo”, depósito de carga bajo el que se encontraban las ruedas hidráulicas. El fondo del banzadillo tenía unos orificios “chiflón” para la salida del agua que se precipitaba sobre las palas de las ruedas. La cantidad de agua que caía sobre la rueda se regulaba desde el interior de la ferrería mediante una palanca. Finalmente el agua una vez cumplida su función propulsora de las ruedas, corría por el canal de desagúe “estolda” para volver al río.
PLANTA
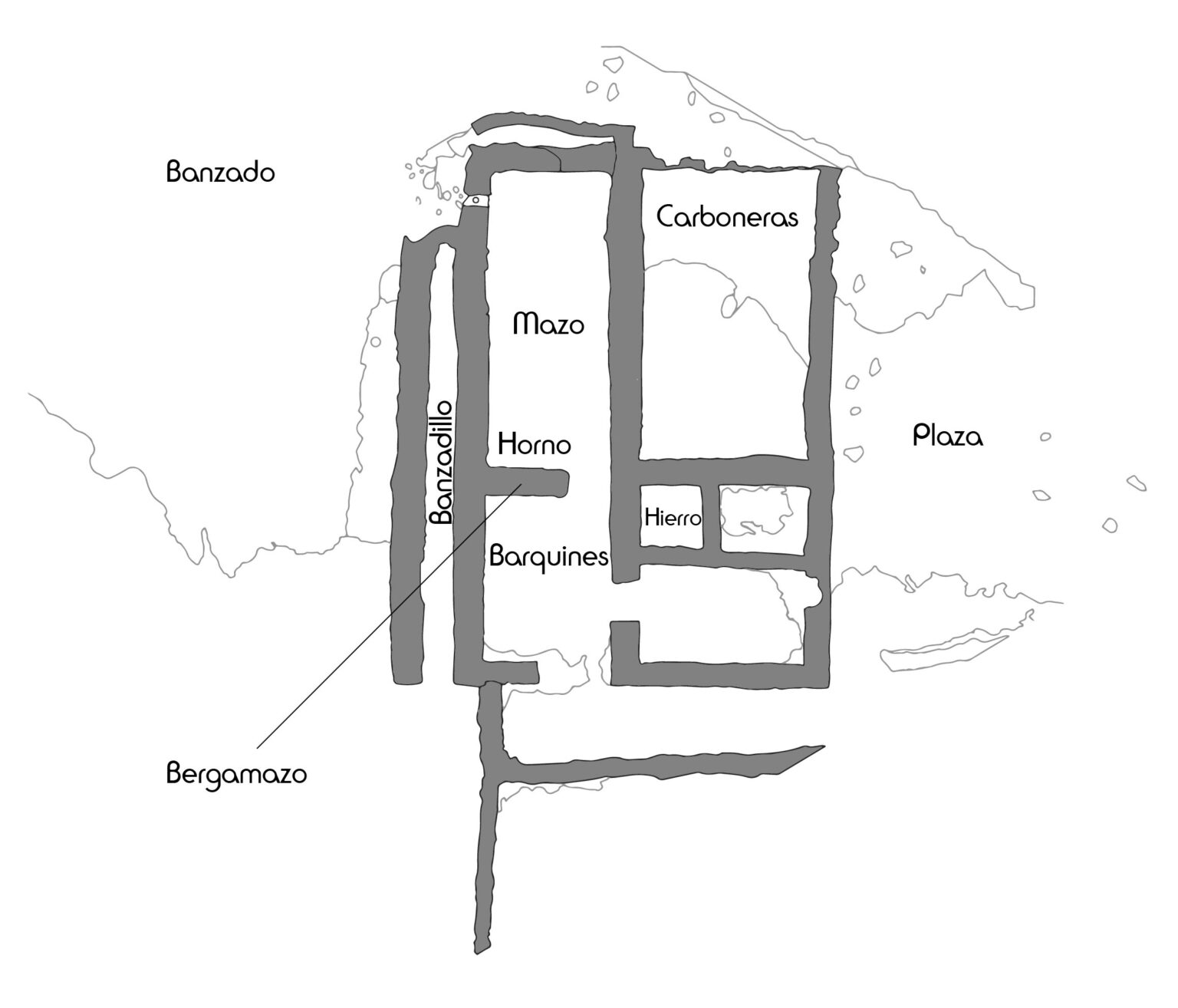
El “bergamazo” dividía el taller en dos recintos: el mayor donde se encontraba el horno y el mazo, y el menor los fuelles o barquines que alimentaban de aire al horno. Esta pared evitaba que el calor del horno afectara la estructura de los fuelles.
El horno, elemento fundamental de la ferrería. En él se realizaba la operación de reducción para convertir el mineral de hierro en hierro. Se introducía el mineral y el carbón vegetal alternándolos en capas. El mineral, previamente, había sido raguado y tazado. La “ragua” consistía en una primera calcinación al aire libre, en la que éste al deshidratarse, facilitaba su reducción permitiendo así al tazador reducir el mineral a trozos pequeños. Para alcanzar la temperatura necesaria en el proceso de reducción, era necesario que el horno tuviera un buen sistema de alimentación de aire. Para ello, se inyectaba aire forzado mediante los fuelles o barquines. El proceso de fundición requería entorno a 4 horas. De aquí se obtenía “la agoa”, pieza compuesta de hierro, escoria, carbón y otros elementos.
Para obtener una pieza de hierro, “la agoa” se sometía a un proceso de martillado en caliente por el mazo (su peso era aproximadamente de 230 kilogramos), que expulsaba la escoria e impurezas y la compactaba conviertiéndola en bandas o barras de hierro. El proceso final era en la fragua, donde el herrero elaboraba o reparaba los productos finales (aperos de labranza, herraduras, clavos, ruedas,…).